We are the technical-commercial partner of the following leaders :
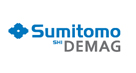
Sumitomo (SHI) Demag was founded in 2008 through the merger of the German group Demag Plastics with the Plastics Machinery division of Sumitomo Heavy Industries, Ltd. In addition to injection molding machines, the industrial division of the Japanese group Sumitomo produces, among others, ships, bridges, mobile cranes, particle accelerators, laser systems, handling equipment and equipment for cancer diagnosis and treatment.
Sumitomo has established an excellent market position in Asia and North America with high performance and technically mature injection molding machines. In the Asian market, one in four electric injection molding machines is a Sumitomo machine.
Since the 1990s, Sumitomo has been focusing on the development and production of electric injection molding machines and is today unquestionably one of the technological leaders in this field. The decisive competitive advantage is the consistent use of know-how and key technologies within the Group, in particular the electric drives specially developed for injection molding.
Since the acquisition of the Demag Plastics Group, the Sumitomo Plastics division has also played an important role in Europe. The merger of the two companies has created the first globally active company in the injection molding industry which is represented on all continents and is a competent partner for its international customers all over the world, without compromise.
400 years of the company’s history show that the Sumitomo Group is not only one of the oldest existing companies, but also the proof of its great willingness to adapt to market requirements. Sumitomo successfully combines tradition with the concentrated innovation strength of the global Sumitomo group.
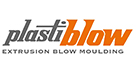
Plastiblow, the automatic world of extrusion blow moulding with low energy consumption.
Electric blowing machines for the food packaging, cosmetic, pharmaceutical, industrial chemical, or detergent sectors. We produce models for every need and size.
50 years of work in blowing extrusion.
Our machines have flexible configurations, reduced energy consumption, constant and precise movements, and reproducibility of machine cycles, with well-defined activity times, a significant reduction in production waste and maintenance response times.
The solutions studied by R&D, today that mechatronics at Plastiblow is a well-established reality, will increasingly aim to integrate the typical functions of a blowing machine with the principles of industry 4.0 of the future digitized society, To develop increasingly efficient and connected systems...
The reliability of Plastiblow machines is demonstrated by the level of export. More than 80% of the machines produced are destined for different countries of the world.
Plastiblow: more than 50 years of quality and Italian expertise in the production of low energy blow extrusion machines.
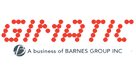
Flexibility, competence, and technology make Gimatic a company at the forefront. This is the winning strategy adopted by Gimatic, a strategy known and appreciated worldwide. The constant desire to grow is what makes it a competitive company and it shows this by investing 10% of its turnover in research and development every year, but also by expanding its activities worldwide.
Gimatic can indeed count on a very dense, organized, and reliable network of distributors and associated companies (10 in total, in Italy and abroad), which are fundamental to guarantee a continuous flow of new products.
This commercial network is used not only to market Gimatic products, but also to receive requests from the user and build an ad hoc solution for any specific application. Gimatic is also synonymous with quality, a characteristic that is guaranteed using innovative and state-of-the-art machines, as well as strict control procedures on both components and finished products.
We have taken the strongest measures to protect the environment, because we see this as part of the fundamental aspects of corporate social responsibility. In addition, we give the utmost respect and consideration to our staff who work every day with passion to achieve our business goals.
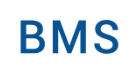
Located in the heart of Europe, between Geneva and Lyon, we have a very large production area with latest generation CNC machines. We design and manufacture a wide range of products and equipment for the plastics industry.
As a logistics platform especially for BMS units in Southern Europe, we have a very large stock of supplies.
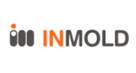
Inmold Plast is a family business, founded in 2006. When we compare the initial and current opportunities in the company and the environment, we find that much has changed, except for the uncompromising quality of our products. This sense of quality, with which we express responsibility for our practices and the market, is present in all phases of our project, from the first communication with the customer, through the development of the product, to its final production. Therefore, we are proud to emphasize that the foundations of our company are superior products, services and customer relationships.
The main activity of Inmold Plast is the production of high-quality tools for injection moulding of plastics and non-ferrous metals. Our specialty is thin-walled packaging injection tools and technical parts injection tools.
In addition to tools, we also manufacture IML robots.
INMOLD owns and successfully implements ISO 9001, ISO 14001 and IATF 16949.
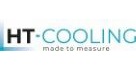
We are professionals with a consolidated experience in the field of process cooling able to offer solutions rather than simple products, to meet the needs of each individual application.
This ability is the result of a 30-year working experience during which we have always focused on solutions, being aware that every process - to be properly faced - must be known .
This is why we present ourselves on the market today in a completely new way compared to our competition, as we do not supply just products but help our customers to identify the perfect technological solution, accompanying them step by step up to the choice of the most suitable system for their application.
We are proud to announce our entry into the Galletti Group, an international reference in the HVAC sector.
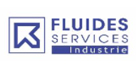
FLUIDES SERVICES INDUSTRIE (FSI) is the synthesis of a long experience, a great passion for work and a creative mind full of ideas.
FSI benefits from significant synergies of «KR Groupe», a group of independent but complementary companies, of which FLUIDES SERVICES is the parent company created in September 1998 by Mr Kamel REBAI, graduate engineer of the Algerian Petroleum Institute (IAP) in 1982 and the National Engineering School of Tunis (ENIT) in 1979.
Highly qualified and highly committed engineers and technicians listen to our customers to best meet their quality requirements while meeting deadlines, standards and health, environmental and safety requirements.
As a subcontractor, we offer our know-how and recognized skills in the following fields:
- Study, design, manufacture, control, and supervision.
- Sheet metal processing, assembly and boile-rmaking.
- Welding and installing piping of all types.
- Installation and assembly of industrial and agri-food factories.
FLUIDES SERVICES INDUSTRIE fabrique et propose une gamme d’appareils et d’accessoires destinés à la plasturgie et développe des solutions personnalisées à la demande de nos clients.
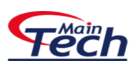
WE COMBINE THE GRIT OF INNOVATION WITH THE COMPETENCE OF TRADITION
Main Tech is a dynamic Italian company that offers a new generation of equipment and complete engineering systems for bulk materials in granules or powder for the plastic, chemical, pharmaceutical and food industry. Launched and managed by people with many years of work in the field, Main Tech combines a culture of innovation with the wisdom of experience to develop its products and services better and better. Located in the North-East of Italy, Main Tech has the advantage of being part of a region influenced by the petrochemical industry since the early 50s, which has led to a radical development and knowledge of operations related to the transport and processing of plastics first and bulk materials in general.
Main Tech designs and manufactures machines dedicated to complete material handling systems as well as storage, material drying, dosing and recycling systems, both for granules and powder materials. The company's young spirit and technical maturity allow Main Tech to meet customer challenges by finding special solutions that are both reliable and cost-effective. Main Tech's competent in-house engineering department takes on new projects and customized turnkey systems, based on specific and special customer needs. In the plastics industry, Main Tech provides dedicated solutions for all applications in extrusion, compounding, rubber production, injection molding, blow molding and roto molding.
MISSION
The company is dedicated to solutions for the plastics processing industry as well as other bulk materials, specializing in the design and construction of machines and complete plants. Main products designed for the handling, processing and dosing of bulk materials and for complete process control of specific applications and niches such as compounding, rubber systems, PVC extrusion, film and filament extrusion processes, injection, blow molding and roto molding, recycling, PET for packaging and part of the food and chemical industries.
VISION
Our presumption is to approach customers as a reliable partner, not just as a supplier. The young spirit of the company, together with the consolidated technical maturation, have allowed us to design and produce systems for the handling and processing of plastic materials, considering crucial the use of quality materials and the development of high technology, with the main objective of meeting the requirements and needs of our customers' applications, aiming to increase their productivity by reducing waste and energy consumption with a consequent increase in the quality of their products. OBJECTIVE: total customer satisfaction! KEY: innovative and reliable quality products, investment in research and development, human resources, quality system, competent and qualified customer service.
CERTIFICATIONS
The quality management system of the Main Tech Srl organization complies with the UNI EN ISO 9001: 2015 standard for the following products/services: Design and manufacture of machines and plants for the processing of plastic materials.

Le groupe Kistler : leader sur le marché de la métrologie dynamique
Aujourd’hui, plus de 60 ans après sa création, le Groupe Kistler est leader mondial dans la métrologie dynamique appliquée à mesurer la pression, la force, le couple et l’accélération. Ne cessant de croître tout au cours des décennies, l’entreprise dirigée par ses propriétaires est passée du simple fabricant de composants au partenaire en développement des sciences et de l’industrie. Nous fournissons des produits mais aussi notre savoir-faire en matière d’applications. Nous sommes toujours restés fidèles à nos racines : près de 2050 collaborateurs répartis sur plus de 60 sites dans le monde développent chaque jour de nouvelles solutions et offrent sur place des services spécifiques aux applications.
Technologie spatiale, sport de compétition ou sécurité des véhicules : les solutions de métrologie Kistler sont toujours de la partie !
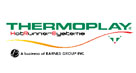
Thermoplay SPA et ses filiales ont été acquises par Barnes Group, Inc., un fabricant international industriel et de construction aérospatial et prestataire de service, en août 2015. Avec cette acquisition Thermoplay rejoint Synventive Molding Solutions et Männer en tant qu’entreprises membres garantissant à Barnes Group la place de leader en plasturgie pour les systèmes d’injection à canaux chauds et l’outillage.
Thermoplay, entreprise spécialisée dans la conception et la production de systèmes d'injection à canaux chauds pour le moulage des matières plastiques. Grâce à sa croissance continue et à d'importants investissements, Thermoplay a rapidement atteint une position leader en Italie et dans le monde entier.
Sa gamme de produits, inclut une offre complète d'injecteurs et de distributeurs standard et spéciaux, des régulateurs de température, des analyses de flux, des projets spéciaux personnalisés, injection simultanée de différents coloris et matériaux pour répondre à tous vos besoins de fabrication destinés à tous marchés et à toutes applications.
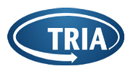
- Passion for the product
- Attention to real customer needs
- Expertise to find the best technical solutions
- Ability to establish relationships with customers, suppliers, partners and company collaborators
These are the values that have defined TRIA’s identity for more than 60 years and contributed to its constant growth.
TRIA wants to be recognized as the most qualified company in the world in the production of blade granulators, in-line recovery systems, crushers, transport systems and treatment of waste generated by the production processes of plastic products .
We continue to cultivate these values, certain that they will increasingly guarantee the satisfaction of all stakeholders and growth in all markets. These characteristics are summarized in the sentence which accompanies the brand:
Your recycling needs. Our grinding solutions.